
The effect of the poor particle/polymer interfacial adhesion bonding of the suspended clay in oil-based mud (OBM) slurry and the LDPE matrix is believed to be the main reason behind the poor thermo-mechanical and mechanical properties of low-density polyethylene (LDPE)/OBM slurry nanocomposites. This study investigates drilling waste valorisation and its use as filler in polymer composites. Traditionally, the drilling waste generated in oil and gas exploration operations, including spent drilling fluid, is disposed of or treated by several methods, including burial pits, landfill sites and various thermal treatments. The effect of filler dispersion in LDPE polymer matrix in relation to thermal stability was investigated and heat capacity data is employed to characterise changes in thermal characteristics relating to the nanomorphology of the materials. An enhancement of mechanical properties of composites was identified which showed a gain of 14% Young’s modulus and a gain of 18% tensile strength at 10.0 wt% OBMFs loading compared to those properties of neat LDPE. The tan δ spectra presented a strong influence of the filler contents on the relaxation process of LDPE and its nanocomposites. Viscoelastic analysis data showed a sharp decrease in the storage modulus of OBMFs reinforced LDPE nanocomposites. The TD5% and TD50% (onset degradation temperature at 5 wt% loss and 50 wt% loss, respectively) of the LDPE nanocomposite with 10.0 wt% OBMFs was the highest (27 ☌ higher in TD5% and 54 ☌ higher in TD50%) among the nanocomposites. The char yields of nanocomposites increased with OBMFs content. It was observed that OBMFs were compatible with LDPE matrix which implies a strong interfacial interaction between the clay layers and polymer and that the influence of clay minerals present in OBMFs formed chemical bonds within the microstructure of the nanocomposites. The effect of reclaimed clay minerals influencing the crystallinity and the dispersion characteristics of this clay in LDPE matrix affecting the structural and thermal properties of the nanocomposites was investigated.

The mechanical testing samples were manufactured using injection moulding.
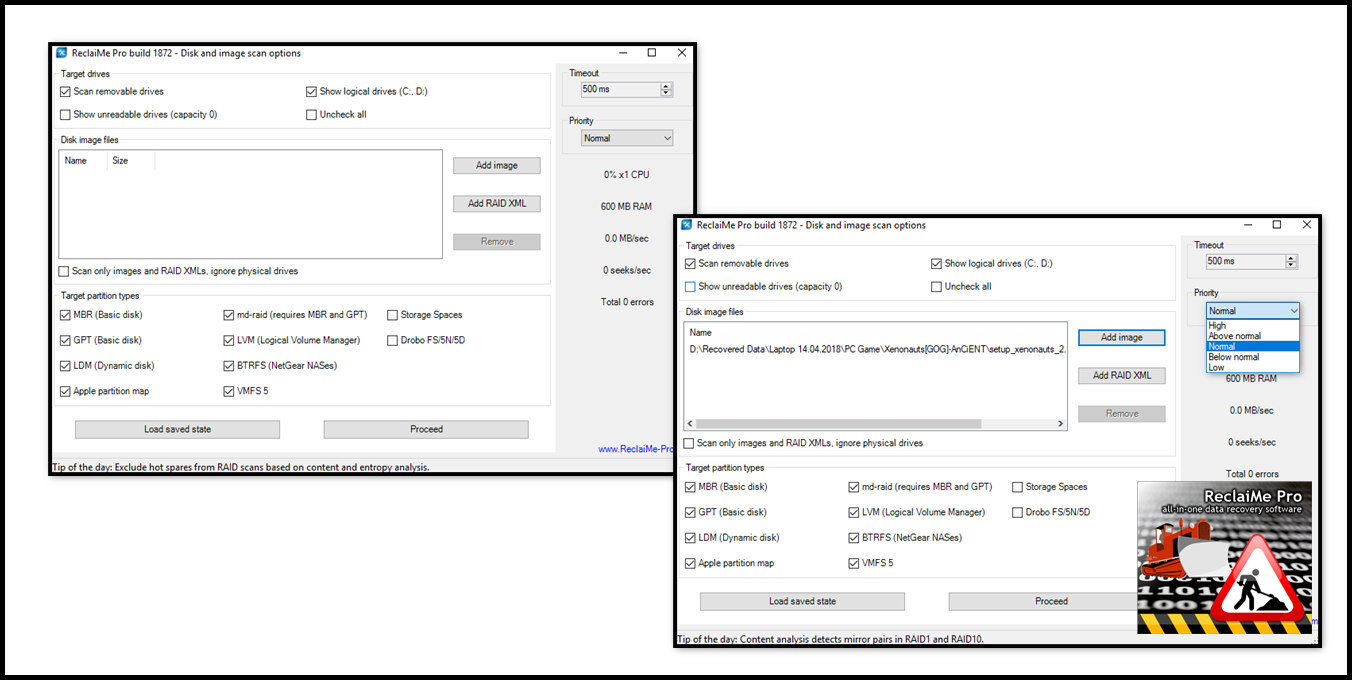
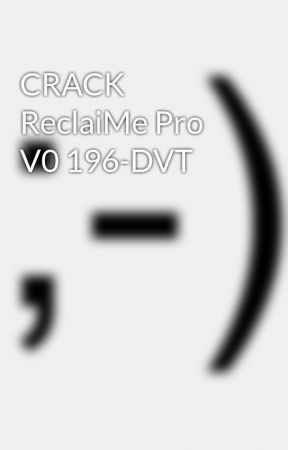
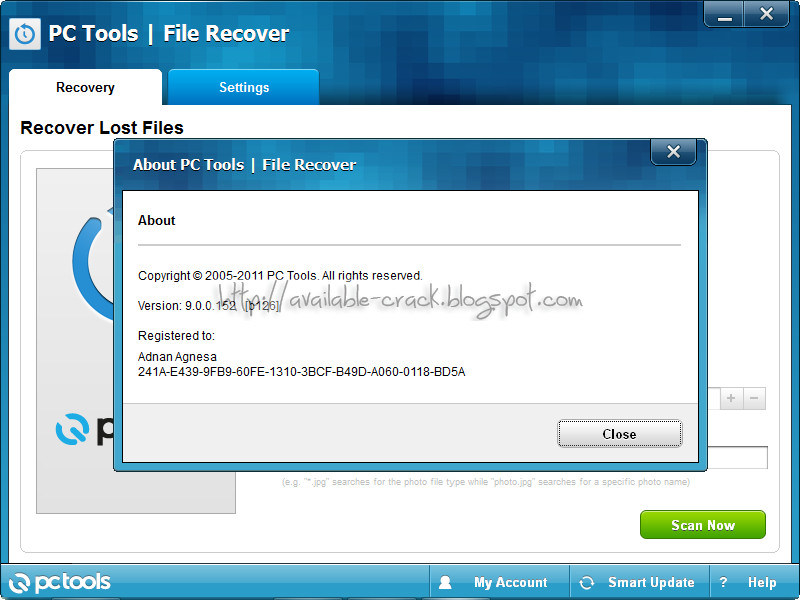
In this study, a novel reclaimed clay nanofiller was used to manufacture low-density polyethylene (LDPE)/Oil based mud filler (OBMF) nanocomposites by a melt compounding process.
